磷化處理對涂層耐腐蝕性的影響,磷化處理對涂層耐腐蝕性能的影響研究
磷化處理是一種通過化學反應(yīng)在金屬表面形成磷酸鹽轉(zhuǎn)化膜的表面處理技術(shù),能夠顯著提升涂層的耐腐蝕性,研究表明,磷化膜作為金屬基體與有機涂層之間的過渡層,不僅增強了涂層與基體的附著力,還通過其微孔結(jié)構(gòu)提高了涂層的封閉性和機械性能,磷化膜的耐蝕性與其成分、結(jié)晶度及厚度密切相關(guān),例如鋅系磷化膜因致密的結(jié)晶結(jié)構(gòu)表現(xiàn)出優(yōu)異的屏障作用,而錳系磷化膜則因較高的硬度進一步提升了抗磨損腐蝕能力,實驗數(shù)據(jù)表明,經(jīng)磷化處理的涂層體系在鹽霧試驗中腐蝕擴展面積可減少50%以上,中性鹽霧測試時間延長2-3倍,磷化膜還能抑制電化學腐蝕的陰極反應(yīng),降低涂層下金屬的腐蝕速率,若磷化工藝控制不當(如溫度、pH或促進劑比例失調(diào)),可能導致膜層疏松或覆蓋率不足,反而加速局部腐蝕,優(yōu)化磷化參數(shù)(如采用低溫細晶化技術(shù))并結(jié)合環(huán)保型無鎳磷化液,已成為當前提升涂層長效防腐性能的研究重點。
磷化處理對涂層耐腐蝕性的影響
磷化處理是一種在金屬表面形成磷酸鹽膜層的化學處理技術(shù),該技術(shù)廣泛應(yīng)用于金屬防腐、涂裝前處理、潤滑和表面裝飾等領(lǐng)域。磷化膜不僅能夠提高金屬本身的耐腐蝕性能,還能顯著提升后續(xù)涂層的附著性和耐久性,從而增強整體防護效果。
磷化膜的作用機制
磷化膜在金屬表面形成后,能夠有效阻止微電池效應(yīng)的發(fā)生,這是導致金屬腐蝕的主要原因之一。此外,磷化膜的多孔結(jié)構(gòu)可以與后續(xù)涂層緊密結(jié)合,提高涂層的附著力,使其更難被腐蝕性介質(zhì)侵蝕。
提高涂層耐腐蝕性的方法
為了進一步提高磷化膜的耐腐蝕性能,從而增強涂層的耐腐蝕性,可以采取以下幾種措施:
優(yōu)化磷化液配方:通過調(diào)整磷化液中主鹽(如磷酸二氫鋅、磷酸二氫錳等)的濃度和比例,合理添加促進劑(如硝酸鹽、亞硝酸鹽、氯酸鹽等),以及加入適量的添加劑(如鎳、鉬、鎢等金屬鹽類或有機化合物),可以獲得結(jié)晶細致、均勻、致密的磷化膜。
控制磷化工藝參數(shù):適當?shù)牧谆瘻囟群蜁r間可以促進磷化膜的形成,但需避免溫度過高導致結(jié)晶粗大,降低膜層的耐腐蝕性。通常,磷化溫度控制在30-60℃之間,磷化時間為2-10分鐘。此外,合理控制酸比(總酸度與游離酸度的比值)也是關(guān)鍵因素之一。
預(yù)處理和后處理:在磷化處理前,對金屬表面進行徹底的除油、除銹、除氧化皮等預(yù)處理,確保金屬表面清潔、均勻。磷化后進行封閉處理,如采用鉻酸鹽封閉、有機涂層封閉等方法,填充磷化膜的孔隙,進一步提高膜層的耐腐蝕性。同時,進行烘干處理,使磷化膜充分干燥、固化,增強膜層的穩(wěn)定性和耐腐蝕性。
清潔生產(chǎn):采用低污染、低能耗的磷化液配方和工藝,減少磷化過程中的有害物質(zhì)排放和能源消耗。加強磷化廢水、廢渣的處理和回收利用,降低對環(huán)境的影響,同時提高資源利用率。
實際應(yīng)用中的效果
在實際應(yīng)用中,通過上述方法優(yōu)化磷化處理工藝,可以顯著提高磷化膜的耐腐蝕性能,進而增強后續(xù)涂層的耐腐蝕性。例如,在汽車緊固件行業(yè)中,通過改進磷化處理工藝,可以使磷化膜在中性鹽霧試驗中達到90分鐘不產(chǎn)生銹蝕的標準,從而提高緊固件的整體耐腐蝕性能。
綜上所述,磷化處理對涂層耐腐蝕性的影響是顯著的。通過優(yōu)化磷化液配方、控制工藝參數(shù)、進行有效的預(yù)處理和后處理,以及采用清潔生產(chǎn)方式,可以大幅提高磷化膜的耐腐蝕性能,從而增強涂層的耐腐蝕性,延長金屬制品的使用壽命。
磷化液配方優(yōu)化的具體步驟
磷化膜耐腐蝕性能測試方法
磷化處理對涂層附著力影響
磷化處理在汽車行業(yè)的應(yīng)用案例
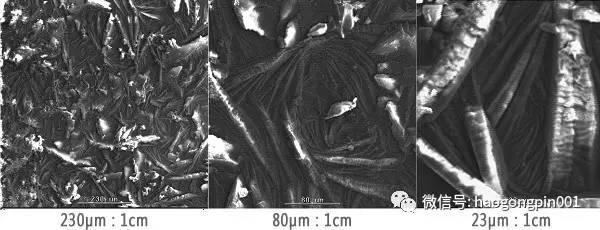
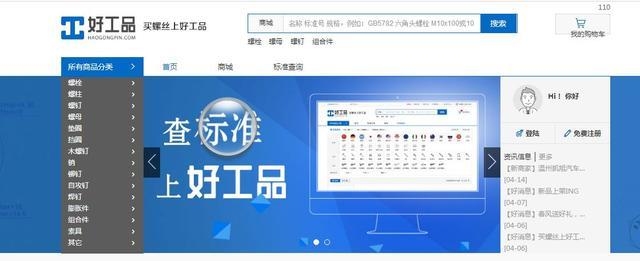
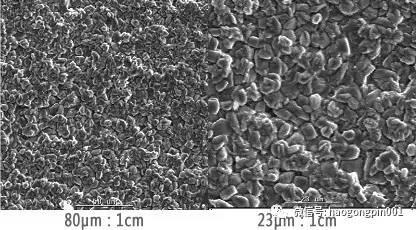
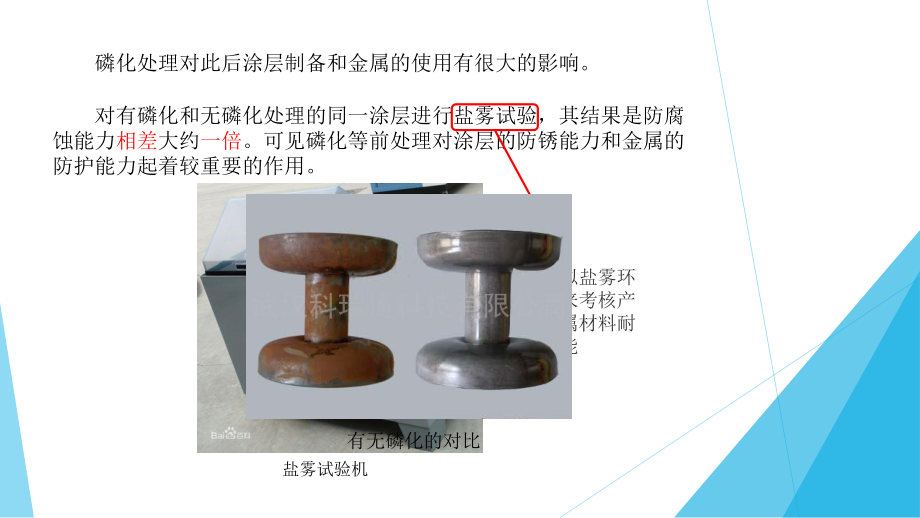
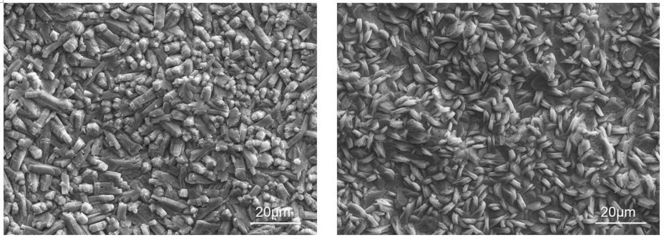
發(fā)表評論
還沒有評論,來說兩句吧...